The same school that originally broke the record for the world’s largest 3D printer in 2019 has just broken its own record.
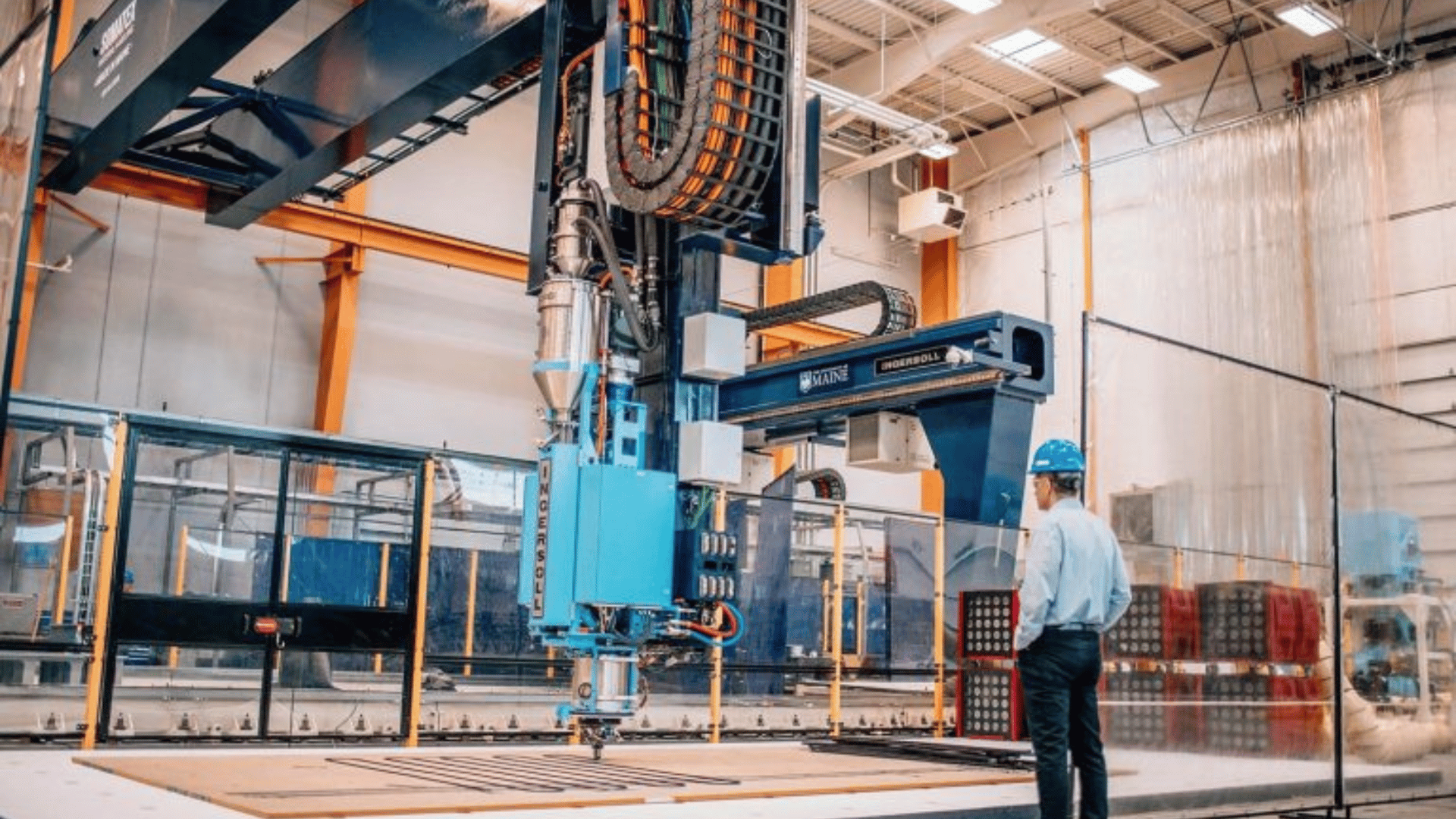
University of Maine designers at the Advanced Structures & Composite Center (ASCC) have revealed their “Factory of the Future 1.0,” or the FoF 1.0. This 3D printer is four times the size of their original Guinness World Record holder, MasterPrint.
FoF 1.0 is capable of printing 96-by-32-by-18-foot tall structures and objects. With such massive printing capabilities, lots of building materials are required as the machine can use upwards of 500 pounds of eco-friendly thermoplastic polymers per hour.
The team’s push to create larger 3D printing machines is inspired by climate change efforts. As global construction projects account for approximately 37 percent of all greenhouse gas emissions, transitioning to sustainable infrastructure projects will go a long way toward lowering emissions.
In addition to creating less emissions by creating houses with more sustainable building processes and materials, 3D printing has the potential to help the environment by building using only the materials needed, which significantly cuts down on waste. It can also save time as the machine models the build beforehand to ensure maximum efficiency.
“There are definitely cost savings with respect to energy efficiency [and] resource efficiency,” says Dr Pei to BBC.
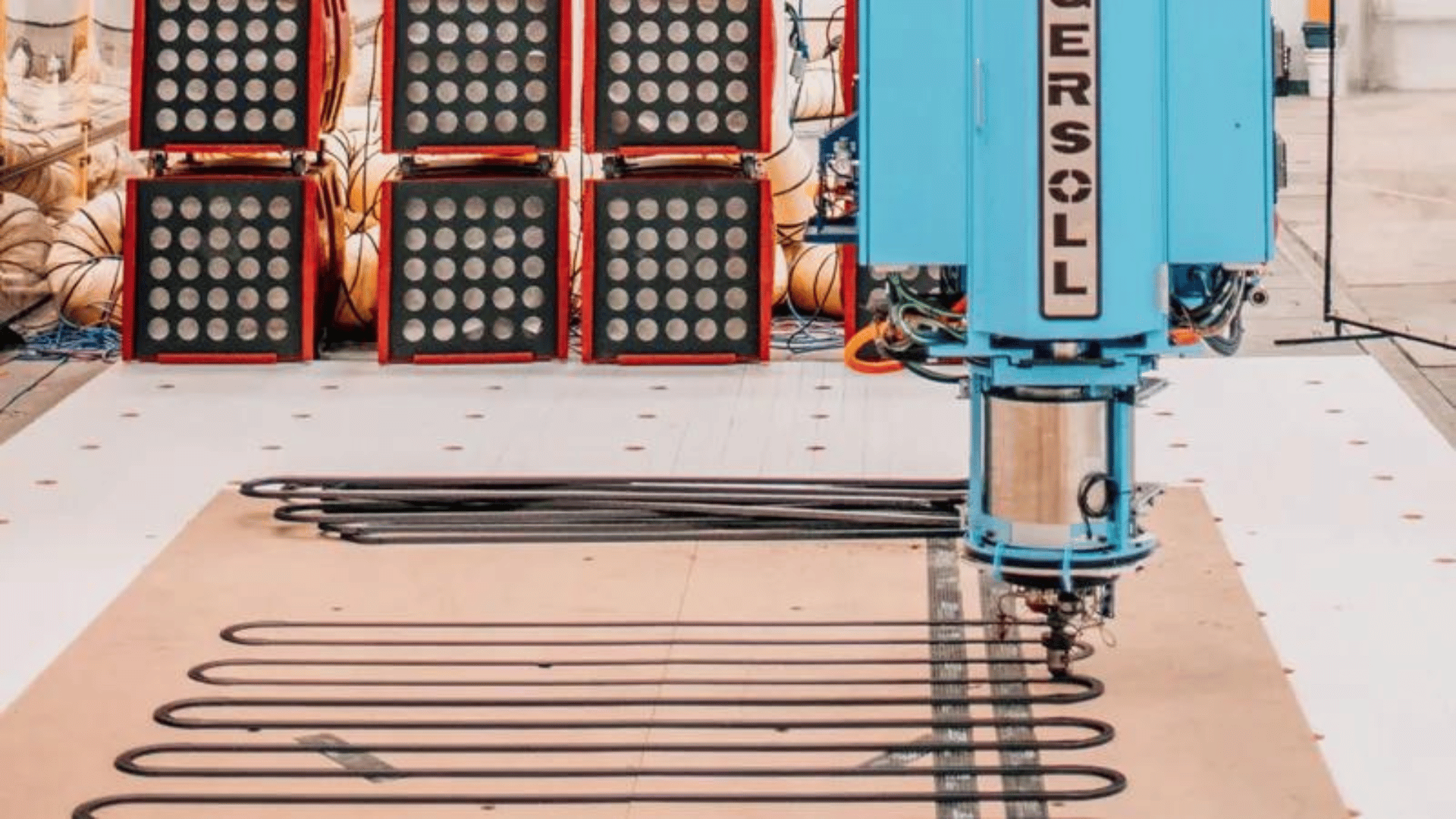
Explore Tomorrow's World from your inbox
Get the latest innovations shaping tomorrow’s world delivered to your inbox!
I understand that by providing my email address, I agree to receive emails from Tomorrow's World Today. I understand that I may opt out of receiving such communications at any time.
The new printer is also designed to work collaboratively with the old record-breaker, Masterprint, as the two machines are capable of working together on the same building components. The ASCC engineers and researchers plan to utilize the printers to help build some of the estimated 80,000 new homes needed in Maine over the next six years.
“It’s not about building a cheap house or a biohome,” ASCC director Habib Dagher said at this week’s event. “We wanted to build a house that people would say, ‘Wow, I really want to live there.’”
According to Dagher, the new machine combines new sensors, high-performance computing, and artificial intelligence. Masterprint is already experienced in this area, having built a sustainable 600-square-foot BioHome3D prototype a few years ago.
The new project’s unveiling event was attended by representatives of the departments of defense, energy, and housing. According to AP, Heidi Shyu, undersecretary of defense for research and engineering, said the printer “stands as a beacon of innovation.”
In addition to printing affordable housing, the University of Maine says it hopes the printer could be used to make boats, bridges, and wind turbines. As the project continues to develop, the team of researchers hopes to experiment with additional bio-based polymer sources, such as residual wood from sawmills in Maine.