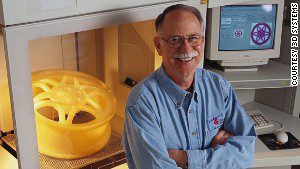
One night in 1983, American engineer Chuck Hull had a breakthrough on his project. His goal was to use his company’s UV lamps to turn designs on a computer into prototypes quickly. Hull experimented with various plastics until he discovered one that would harden nearly instantly under UV light. At that moment, 3D printing was born.
Since its invention, 3D printing has grown from something purely for professionals to a fairly common household appliance. Of course, members of the manufacturing industry are still the most likely to have access to and use the device. In a 2017 report published by online 3D printing company Sculpteo, 55% of respondents “predict they will be spending more in 3D Printing services and solutions.” And considering the cost of even consumer-grade printers, the focus on appealing to the industry is only logical.
For professionals, the most common application of 3D printing is creating prototypes and proofs of concept, just as Hull did 35 years ago. Sculpteo’s report shows that 57% of respondents use it in one of those two categories (full graph below). However, respondents in both America and Europe cite multiple “main benefits” from utilizing 3D printing technology. This focus on research and development is reducing overall concept-to-market time. Consumers are able to get their products faster thanks to the 3D printing process.
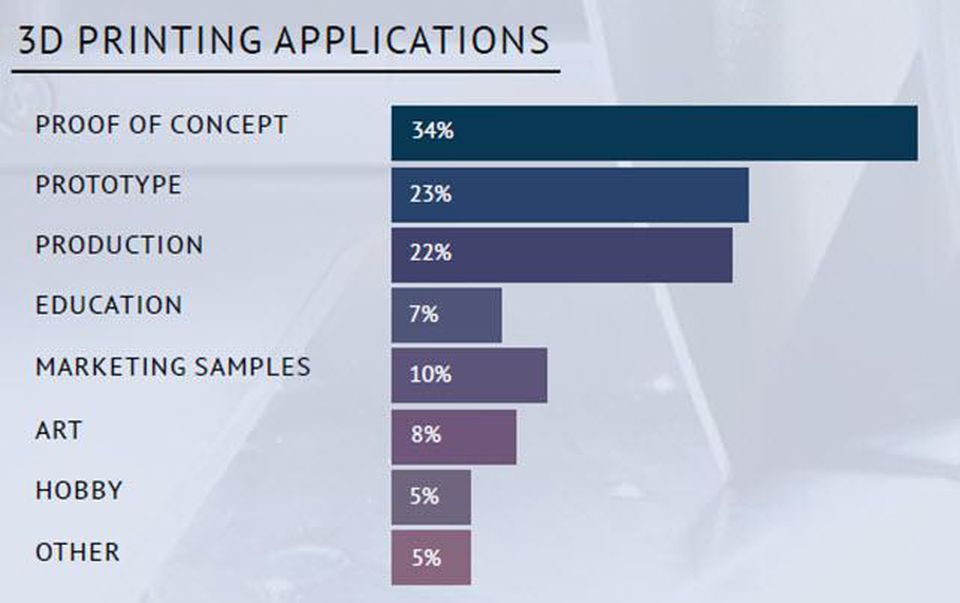
It’s also giving smaller-scale artisans access to borderline mass-production technology. Sculptors and designers are able to make their creations for cheaper and using less time than if they used traditional methods. Creating custom accessories and costume pieces no longer requires hours of construction, just some plastic and a computer program. It is not cutting into the traditional arts by any means, but rather giving artists more options and flexibility within their craft.
In an interview with CNN, Hull reveals how pleased he is with the 3D printing revolution. When asked when he first saw 3D printing taking off, he replied: “Well, it’s really blossomed just in the last few years- in the sense of really rapid growth and recognition. There’s a lot of things that contribute to that, I think: a lot of medical applications catch peoples’ imagination; certainly the maker movement, with low-cost machines getting hobbyists interested in inventing and building using 3D printing.”
Those medical applications include creating everything from cost-effective prosthetics to custom implants. The story of the baby born with a defective trachea took the world by storm in 2015. Even with traditional surgery, the trachea collapsed from being so weak. The surgical team created a replacement trachea using 3D printing that was molded especially for the infant and would eventually absorb the existing, damaged trachea. Other common uses in the medical industry include creating devices like hearing aids and eyeglasses.
The real breakthrough, however, is still in its infancy. Using 3D printing technology to create new organs is not a new concept, but only now is it even nearing feasible. Structures like blood vessels, bones, and the bladder have already been produced, but more complex organs are still on their way (but closer than ever). Says Dr. Justin Ryan, a biomedical engineer and research scientist at Phoenix Children’s Hospital, “part of the challenge of printing complex organs is that organs need oxygen and nutrients.” He described the main problem is being able to print organs and blood vessels at the same time to ASME. “Outside of that, it’s also the concept than an organ isn’t just tissue but what you might loosely refer to as memory, so your heart isn’t just a collection of cells, it’s also the tissue that supports the tissues that lead to thousands and thousands of heartbeats.”
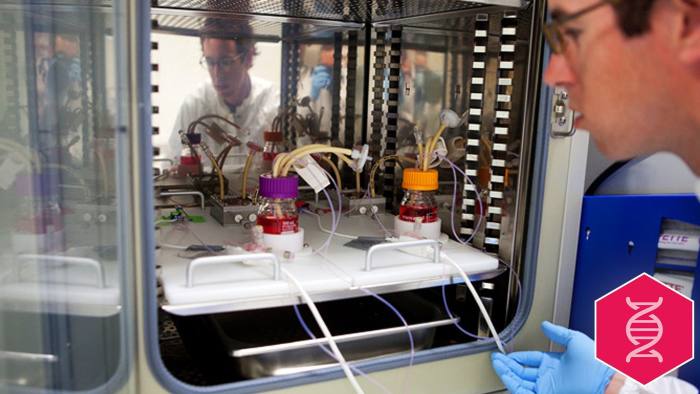
Progress is being made, though. In March, San Diego company Organovo was able to print a working liver. The liver, as the most regenerative organ in the human body, is the perfect stepping stone to larger, more complex organs. But mastering liver printing is vital in its own right. For now, the cells in 3D printed livers don’t survive past a year. Professor David Hay of the University of Edinburgh told the Financial Times “the short to midterm goal would be looking at a ‘bridge’ to transplant. The long-term objective would be to create a liver implant that can provide liver support for longer.”
If using human tissue isn’t vital, however, using silicone or other soft materials to make replacement organs is a thriving field. Scientists in Switzerland were able to print an artificial heart in July of 2017- one that can beat almost identically to how a human heart does. Due to the nature of the printing, these hearts can be exact copies of the organs they’re replacing. However, they only last about 3000 beats before failure, making them extremely short-term solutions (for reference, the average 40-year-old’s BPM is 90-153).
Still, it’s all very promising. Millions of people worldwide need organ transplants each year, but the number of donors never matches the demand. Mastering the science behind printing organs will eliminate the need for transplants at all and will save countless lives. It’s still years, maybe even decades, from being safely doable, but the advances being made prove that it’s possible. 3D printing still provides plenty of benefits to medical professionals until then. Says Hull to CNN, “as soon as I started working with some of the medical imaging people, it became pretty clear that this was going to work.”
For technology available already, turn back to the consumer side of things. For those without the space or funds to buy a full 3D printer, 3D printing pens offer an alternative. They can’t create objects as complex as 3D printers and are more geared towards artists than hobbyists. Essentially, these pens are able to write and draw in all three dimensions, using plastic filaments in lieu of ink. They do get hot and can be a bit hefty- think of a hot glue gun on steroids. However, there’s a large variety on the market geared towards veterans to newbies and everybody in between. Almost all of the pens found online retail for under $100, making them perfect budget options and a first taste of what 3D printing is capable of.
Alternatively, one could ask a 3D printing shop to take care of the printing for you. Much like traditional print shops, these take the designs given to them and print them to your specifications. It’s not a logical solution if you have to make multiple versions of one design, but for custom, singular pieces, the only better option is asking a friend with a 3D printer to print it. These print shops do offer some features consumer-grade printing does not: higher quality printers, ability to print larger objects, and maybe even the ability to print using metal instead of plastics. There are plenty available online (like the aforementioned Sculpteo) but physical locations are cropping up worldwide.
And the things that these companies can create is astounding. Recently, Silicon Valley startup Arevo Inc created a carbon fiber bicycle. It may not sound impressive, but the frame was created using a 3D printer. Normally, carbon fiber bicycles are tremendously expensive due to the human labor and work conditions required to build it. Arevo’s bikes, on the other hand, are made for about $300.
Bikes aren’t really a human necessity, not in the same way shelter is. Companies with oversized 3D printers are able to print out entire houses in less than 24 hours for a mere $10,000. These homes contain a living room, bathroom, kitchen, bedroom, and even a shaded porch. Housing startup ICON and nonprofit New Story are working on bringing this technology to El Salvador and then create a 100-home community. These versions will only cost $4000 per house and would be a huge improvement over the lean-tos and huts many people worldwide currently reside in.
Or, if you wish to become part cyborg, you could have 3D printing applied directly to your skin. Researchers at the University of Minnesota have devised a way to place electronics on a person’s hand completely safely (and for less than $400). Michael McAlpine, a study lead on the project, told CNet “we imagine that a soldier could pull this printer out of a backpack and print a chemical sensor or other electronics they need, directly on the skin. It would be like a ‘Swiss Army Knife’ of the future with everything they need all in one portable printing tool.” It’s not just electronics that can be applied- it can print out skin cells for easy grafting, even if the user is moving.
Hundreds of other stories on 3D printing are available online. Smart gel that walks underwater? Stylish sneakers? Formula One racing cars? Nearly everything is able to be printed, and it’s revolutionizing the world. Durable and vital products can now be produced for cheap, making them easier to access for anybody, no matter their means. Even things like fabric and wood can be printed, meaning it’s not just plastics and metals that can be manufactured.
And it all began with Chuck Hull and him experimenting with photopolymers and UV light. Yes, the process has changed quite a bit since he first brainstormed the idea. “One of the most significant [changes] is the basic accuracy you can achieve,” he told CNN. “Because [the materials] cure from a liquid to a solid, they tend to shrink and they can distort. So as you build these 3D parts you get some inaccuracies and warp-age [sic]. But that chemistry has been vastly improved, so there’s almost no distortion now. Also the physical properties: initially the materials were very brittle… nowadays you get really good, tough plastic materials.”
Hull isn’t even sure if the 3D printing revolution will ever slow down. “There’s limits to everything. So, the kind of traditional limits 3D printing have been: material properties, making millions of things… [but] it looks like those limits are going to be beat down over the next few years.” With an estimated $12 billion to be spent on 3D printing in 2018, it’s only logical that companies will want to make printing as efficient and limitless as possible.
Be it consumer or commercial, 3D printing is a juggernaut that has impacted the production and manufacturing industry immensely. It’s entirely possible it may shake the world the same way factories did over a hundred years ago. The similarities are striking: both have made creating and selling items of all kinds easier and more affordable. And it all began with one man messing around with plastics and ultraviolet lights. Could he ever imagine this happening?
Chuck Hull laughs. “Not at the consumer level, [at least,]” he says.
Follow our World of Production on Instagram–where big ideas bring big growth.